Zinc-Heavy Epoxy Primer: A Comprehensive Technical Manual
Overview
Industrial and construction settings frequently use zinc-rich epoxy primer, a high-performance coating method, to prevent corrosion on metal surfaces. Its special composition creates an efficient barrier against environmental degradation by fusing the durability of epoxy resins with the rust-inhibiting qualities of zinc. Zinc Rich Epoxy Primer-This extensive book provides insightful information for experts across a range of industries, covering in detail the composition, advantages, uses, and best practices for applying zinc-rich epoxy primer.

Zinc-Rich Epoxy Primer: What is it?-Zinc Rich Epoxy Primer
Zinc-rich epoxy primer is a unique kind of coating made of a blend of epoxy resin and zinc dust. As a sacrificial anode, the zinc dust corrodes preferentially to shield the metal substrate underneath. The epoxy resin enhances the primer’s durability and chemical resistance, while also forming a robust adhesive bond. Together, they provide a strong protective coating that keeps metal structures from rusting and prolongs their lives.
Make-Up
1. Epoxy Resin: The primary binder in zinc-rich primers is epoxy resin. They are reputed to having outstanding mechanical strength, adhesion, and resistance to chemicals and environmental elements. The epoxy resin encasing the particles of zinc dust forms a strong, protective layer.
2. Zinc Dust: Zinc dust is an essential part of primer that gives the metal surface cathodic protection. Tiny zinc particles, when applied, cover the substrate in a conductive layer. This layer corrodes instead of the underlying metal, preventing rust.
3. Additives: To enhance the primer’s qualities, we add a variety of additives such as thickeners, curing agents, and wetting agents. These additions enhance the primer’s durability, application qualities, and overall performance.
4. Solvents: Solvents change the viscosity of the material to make primer application easier. After application, they vanish, leaving a strong layer of protection behind. The solvent selection may impact the application technique and drying time.
Qualities-Zinc Rich Epoxy Primer
1. Corrosion Resistance: The zinc-rich epoxy primer’s main advantage is its enhanced corrosion resistance. Zinc particles protect the metal substrate from corrosion and deterioration by acting as a sacrificial layer.
2. Adhesion: The epoxy resin sticks to metal surfaces very well, creating a solid connection that keeps the primer in place even under the most adverse circumstances.
3. Durability: Epoxy primers that are high in zinc are renowned for their resilience to abrasion, impact, and chemical exposure. This resilience allows their use in challenging settings.
4.Drying and Curing: These primers typically dry quickly, which speeds up project completion. Environmental factors like humidity and temperature might affect how long a cure takes.
The benefits of zinc-rich epoxy primers-Zinc Rich Epoxy Primer
1. Improved Corrosion Protection: The primer’s high zinc concentration offers better defense against rust and corrosion. This is especially useful in areas where there is a lot of dampness, salt, or chemical exposure.
2. Extended Service Life: Zinc-rich epoxy primers help structures and equipment last longer by preventing corrosion on metal surfaces. As a result, less regular maintenance and replacements are required.
3. Versatility: Zinc-rich epoxy primers have a wide range of applications, including industrial, infrastructural, and maritime projects. Their adaptability makes them a top option for a wide range of metal surfaces.
4. Cost-Effectiveness: Although zinc-rich epoxy primers may initially cost more than certain other coatings, they are a more cost-effective option in the long run due to their longer lifespan and lower maintenance requirements.
5. Application Ease: There are several ways to apply the primer, including rolling, brushing, and spraying. Its adaptability allows for its use in a variety of project sizes and specifications.
Uses
1. Marine Industry: Epoxy primers with a high zinc content protect ships, offshore platforms, and other structures exposed to seawater. The primer’s ability to resist corrosion is critical for preserving these resources’ integrity.
2. Industrial Facilities: Zinc-rich epoxy primers frequently coat pipelines, tanks, and structural steel in industrial environments. They offer crucial defense against caustic substances and challenging working environments.
3. Infrastructure Projects: Zinc-rich epoxy primers offer long-lasting protection for bridges, roads, and other infrastructure projects. These coatings enhance the longevity and safety of critical infrastructure.
4. Architectural Steel: Zinc-rich epoxy primers provide a long-lasting protective coating that improves the look and lifespan of steel components used in buildings and other architectural projects.
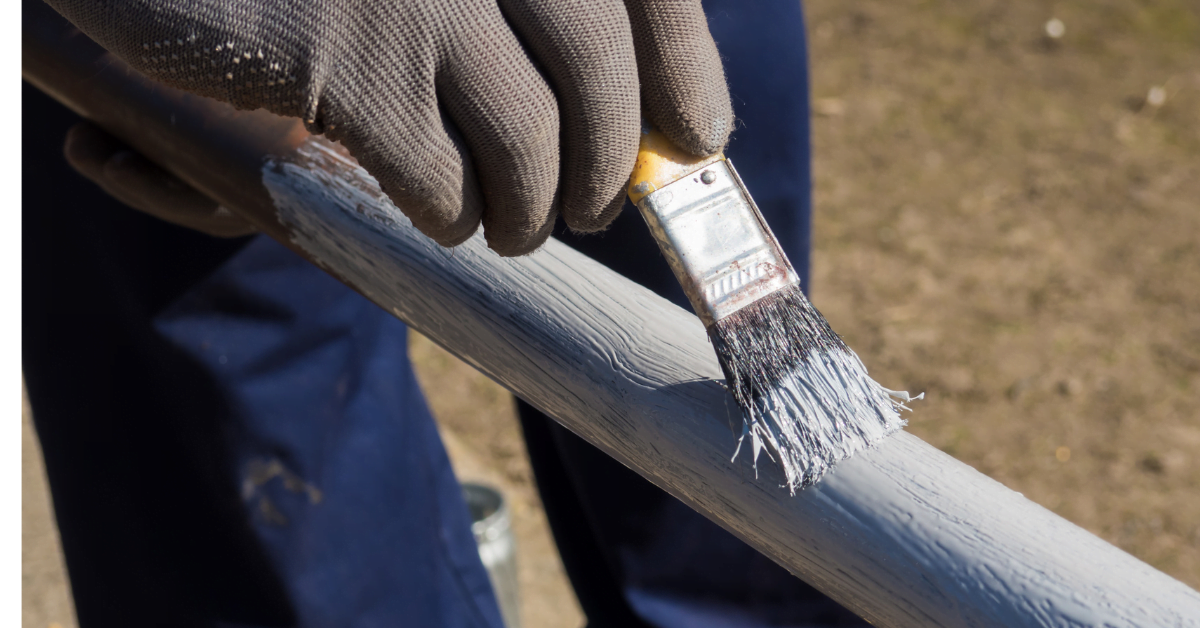
Techniques of Application
Surface Readiness
You must properly prepare the surface for zinc-rich epoxy primers to work as intended. The surface needs to be clear of impurities, dry, and clean.
1. Cleaning: Use mechanical or abrasive blasting techniques to remove old coatings, mill scale, and rust. By doing this, you can be confident that the primer will properly stick to the metal surface.
2.Degreasing: Use the proper solvents to clean the surface and get rid of any oil, grease, or other impurities that might hinder adhesion.
3. Inspection: Prior to using primer, make sure the surface is totally dry. Moisture might hinder both adhesion and general performance.
Combining and Using
1. Mixing: In accordance with the manufacturer’s instructions, thoroughly combine the zinc dust and epoxy resin. Proper mixing guarantees consistent performance and even dispersion of zinc particles.
2. Application: Depending on the needs of the project, apply the primer with a roller, brush, or spray gun. It could take many applications to get the thickness and coverage that you want.
3.Curing: Let the primer cure in accordance with the guidelines provided by the manufacturer. Temperature and humidity are two examples of variables that might affect the curing period. Make sure that nothing disturbs the covered surface while it cures.
Safety Points to Remember
1. Ventilation: To avoid fume accumulation and preserve air quality, make sure there is enough ventilation during application. This is especially crucial in places that are small or have little ventilation.
2. Protection Gear: To guard against exposure to chemicals and dust, put on the proper personal protection equipment, such as respirators, goggles, and gloves.
3. Disposal: Take care to dispose of empty containers and leftover primer in accordance with local laws. Proper disposal has two benefits: ensuring regulatory compliance and reducing environmental damage.
Zinc-rich epoxy primer types
1. Inorganic zinc-rich epoxy primer, known for its exceptional durability and heat resistance, includes zinc oxide or zinc silicate. It works well in situations with a lot of chemical exposure and high temperatures
2. Zinc dust and epoxy resin are combined to create Epoxy Zinc-Rich Primer, which is extensively utilized because of its general corrosion resistance and good adhesion. It works well in many different environments and application areas
Typical mistakes to avoid.
1. Insufficient Surface Preparation: Improper surface cleaning and preparation can lead to poor primer adherence and decreased efficacy.
2. Inaccurate Mixing Ratios: Improper mixing of zinc dust and resin can lead to uneven performance and reduced corrosion protection.
3. Ignoring safety precautions: Not wearing the right PPE and making sure there is enough ventilation can expose people to dangerous substances and put their health at risk.
4. Ignoring Manufacturer Instructions: To get the best results and guarantee the primer’s efficacy, always adhere to the manufacturer’s instructions for mixing, applying, and curing.
Advanced Zinc-Rich Epoxy Primer Formulation Methods
Zinc-rich Epoxy Primers: Nanotechnology in Action
By adding nanoscale components, recent developments in nanotechnology have improved the effectiveness of zinc-rich epoxy primers. Nanoparticles like carbon nanotubes or nanosilica enhance properties like adhesion, scratch resistance, and UV stability. These nano-additives can increase the uniformity of the coating, decrease the primer’s permeability, and prolong the protective layer’s lifespan.
Superior-Grade Fillers and Pigments
High-performance colors and fillers can enhance the appearance and performance of zinc-rich epoxy primers. For example, high-tech pigments can increase color retention and fade resistance, while specialty fillers can improve the impact resistance and general longevity of primer. These additions allow us to tailor the primer to meet specific performance standards and aesthetic specifications.
The impact of sustainability on the environment
Substitutes that are low-volume and sustainable
The creation of environmentally friendly, low-VOC (volatile organic compound) epoxy primers that are high in zinc has taken precedence due to increased environmental concerns. These formulations limit their influence on the environment and reduce hazardous emissions. Manufacturers are investigating alternative resins and solvents that preserve performance and are more ecologically friendly. Manufacturers can use low-VOC goods by adhering to stricter rules and promoting a better work environment.
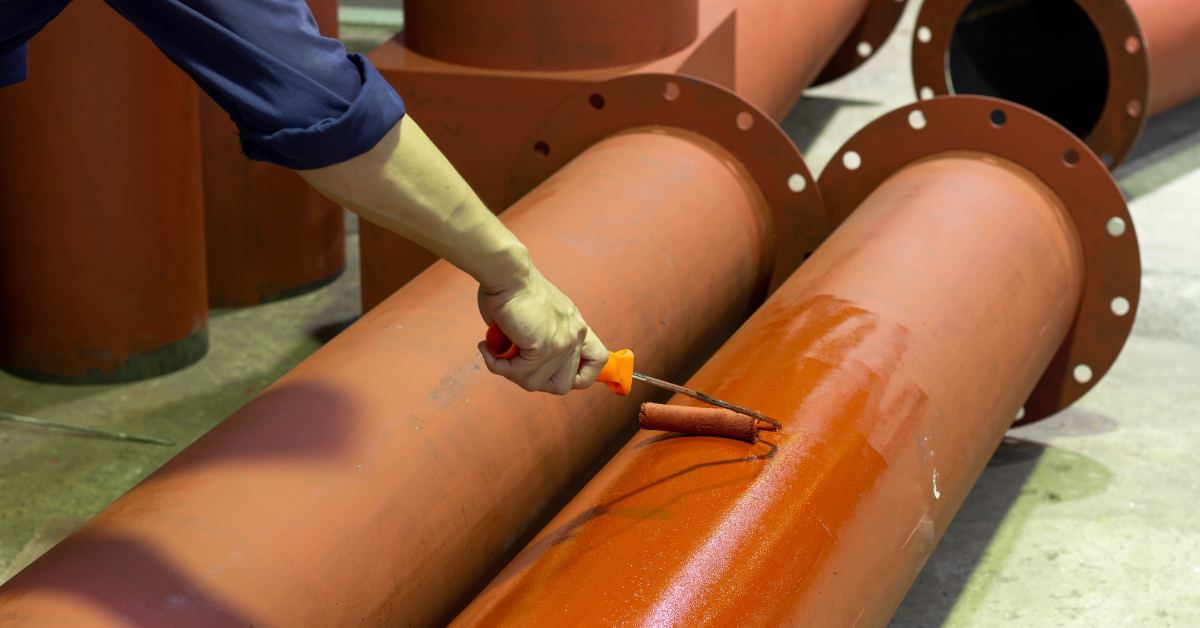
Waste Management and Recycling Techniques
Recycled materials and waste handling are essential to reducing the environmental impact of zinc-rich epoxy primers. Numerous producers are putting procedures in place to properly handle waste materials and recycle leftover primer. This entails creating primer residue recycling programs and repurposing packing materials. Using these techniques encourages resource sustainability and lessens the impact on the environment.
Novelties in Application Methods
Robotic and automated application systems
Zinc-rich epoxy primer utilization is changing due to automation and robots, particularly in large-scale industrial and infrastructural projects. Automated systems can apply primers with extreme uniformity and accuracy, reducing labor costs and application errors. These technologies are especially helpful in settings where manual application is risky or difficult.
Cutting-Edge Spraying Technologies
The development of sophisticated spraying techniques, such as airless and electrostatic spraying, increases application coverage and efficiency. To provide consistent coverage and minimize overspray, electrostatic spraying employs an electrical charge to draw primer particles to the substrate. However, airless spraying works well on larger surfaces because it can apply thicker layers more quickly.
Methods for Testing and Quality Assurance
Quick Corrosion Examination
Accelerated corrosion testing techniques test zinc-rich epoxy primers under harsh circumstances. These tests evaluate the endurance and efficacy of the primer by simulating extreme circumstances such as high humidity, salt spray, and UV exposure. Understanding the results of these experiments helps producers refine formulas and ensure that primers meet industry requirements.
Testing for adhesion and impact resistance
Testing for adhesion and impact resistance is necessary to determine the quality of zinc-rich epoxy primers. Impact resistance tests assess the primer’s capacity to endure physical impacts without peeling or splitting, whereas adhesion tests assess how effectively the primer adheres to the metal surface. These tests aid in confirming that the primer offers dependable protection and operates effectively in practical settings.
Prospective Patterns and Advancements
Self-healing technologies and intelligent coatings
Zinc-rich epoxy primers of the future could incorporate self-healing technology and intelligent coatings. Engineers have engineered smart coatings to react to variations in temperature and humidity in the surrounding air by changing their characteristics or hue. By using self-healing technology, the primer can automatically fix minor damage and continue to provide protection over time.
IoT Integration for Monitoring
The combination of Internet of Things (IoT) technologies with zinc-rich epoxy primers is an emerging trend. Real-time monitoring of variables including temperature, humidity, and corrosion levels is possible with IoT sensors integrated into coatings. With this information, one can evaluate the primer’s effectiveness and decide on necessary upkeep and repairs.
Compliance with regulatory standards
Industry Requirements for Epoxy Primers Rich in Zinc
Zinc-rich epoxy primers must adhere to a number of industry norms and guidelines in order to guarantee their quality and security. Standards for primer performance and corrosion protection include SSPC-Paint 20 and ISO 12944. Adherence to these guidelines aids in guaranteeing that the primer fulfills the essential criteria for robustness, security, and ecological footprint.
Safety Data Sheets and Labeling (SDS)
Safety Data Sheets (SDS) and proper labeling must inform users about the safe handling and application of zinc-rich epoxy primers. The SDS papers provide comprehensive information on the primer’s dangers, composition, and safety measures. Maintaining correct and up-to-date SDS and labeling aids in preventing abuse and encourages safe behaviors.
User Advice and Optimal Techniques
Enhancing the Performance of Primer
Users should follow best practices, such as maintaining appropriate surface preparation, making sure mixing ratios are accurate, and applying the primer under suggested circumstances, to maximize the effectiveness of zinc-rich epoxy primers. Additionally, routine inspections and maintenance may ensure that the primer continues to provide reliable protection by identifying problems early on.
Education and Talent Acquisition
It is critical to allocate resources to the training and skill enhancement of individuals who apply zinc-rich epoxy primers. Applicators who have received the appropriate training will know the primer’s safety precautions, application methods, and characteristics. This could lead to better application outcomes and a safer workplace.
In summary
Zinc-rich epoxy primer is an excellent coating option for preventing corrosion on metal surfaces and prolonging the lives of many types of buildings. Its special blend of epoxy resin and zinc dust offers remarkable durability, corrosion resistance, and adaptability. Professionals may use zinc-rich epoxy primer to achieve the best results in their projects if they are aware of its composition, advantages, uses, and best practices. Ensuring long-term protection and optimizing the primer’s function need careful surface preparation, application methods, and safety precautions.
FAQ:
What is an epoxy primer with high zinc content?
A zinc-rich epoxy primer is a high-performance coating that typically contains 60–90% zinc dust by weight. This primer offers superior corrosion protection for steel and other metal surfaces. By corroding preferentially, the zinc serves as a sacrificial anode, preventing corrosion and deterioration of the underlying metal
What are the primary uses for zinc-rich epoxy primer?
Many industrial and construction contexts use zinc-rich epoxy primers when a high level of corrosion resistance is crucial. Bridges, pipelines, industrial facilities, maritime locations, and steel buildings exposed to inclement weather are examples of common uses. Surfaces exposed to chemicals, dampness, or high temperatures, which are susceptible to corrosion, are ideal for their use
How is zinc-rich epoxy primer applied?
Applying zinc-rich epoxy primer requires a few crucial steps:
Surface Preparation: Make sure the surface is free of debris, oil, and corrosion, as well as dry and clean. People frequently employ mechanical cleaning techniques like abrasive blasting.
Mixing: Before applying the primer, thoroughly combine the ingredients according to the manufacturer’s recommendations.
Application: Use a brush, roller, or spray gun to apply the primer. Many coats may be required, depending on the desired thickness and the state of the surface.
Curing: Prior to applying any topcoats or subjecting the surface to service conditions, let the primer cure in accordance with the manufacturer’s recommendations-Zinc Rich Epoxy Primer.
What advantages do epoxy primers with a high zinc content have over other primer types?
Zinc-rich epoxy primers have a number of benefits.
Superior Corrosion Resistance: Suitable for severe situations, the high zinc concentration offers exceptional protection against rust and corrosion.
Adhesion: They may serve as a foundation for different topcoats and stick to steel surfaces with excellent adherence.
Durability: They can tolerate physical wear and tear and have excellent abrasion resistance
In contrast, other types of primers could not offer as much durability or galvanic protection-Zinc Rich Epoxy Primer.
Are zinc-rich epoxy primers related to any safety or environmental issues?
There are a few things to consider:
Health Risks: When applied, zinc-rich primers may create toxic fumes. Wearing the proper personal protective equipment (PPE), such as gloves and respirators, is crucial.
influence on the environment: In order to reduce the influence on the environment, remaining primer and cleaning solutions must be disposed of properly. Observe local laws while disposing of hazardous garbage.